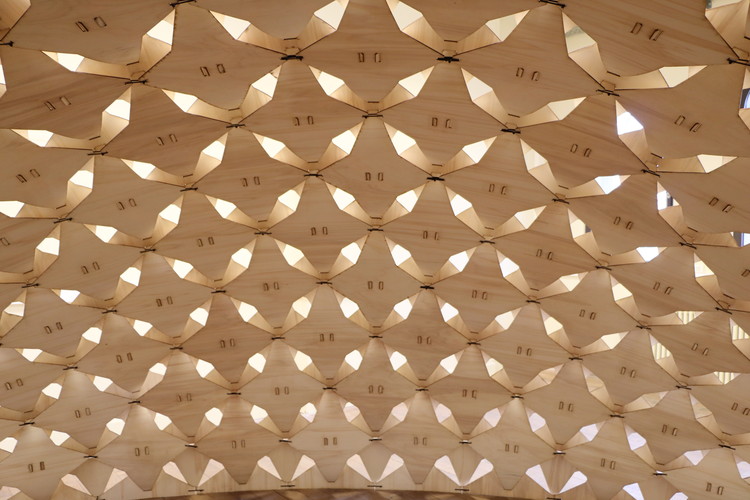
"Exoskeleton(外骨骼)" 展示了计算机辅助制造如何创造快速原型。这个制造过程可以利用有限的资源进行实际规模的建设和试验。
在这个项目中,被设计成不同尺度的模块系统利用简单的连接件连接,而不使用钉子和螺丝。这样就可以形成不同的表面,并且可以在不同的角度和高度上进行旋转和组合。
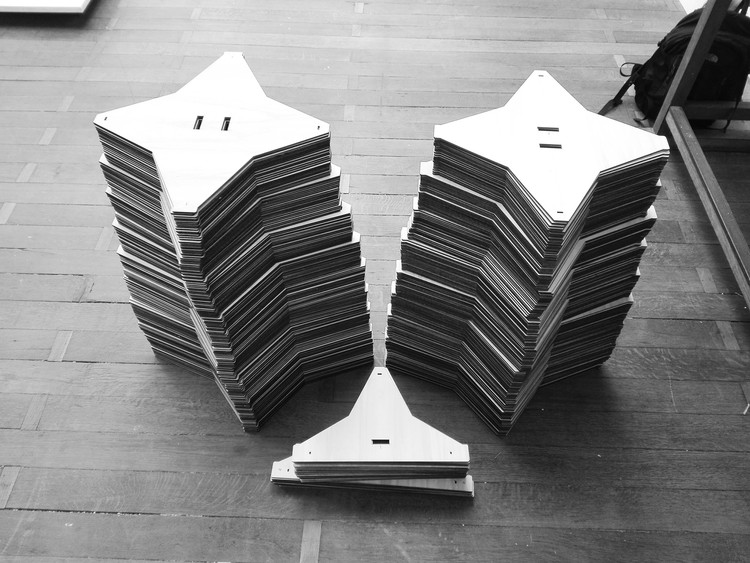
来自建筑师。我们的硕士论文研究了一种“自下而上”的结构设计方法,即通过原型设计,是数字制造的一个分支。这个小亭子的设计“外骨骼”作为一个测试范例。
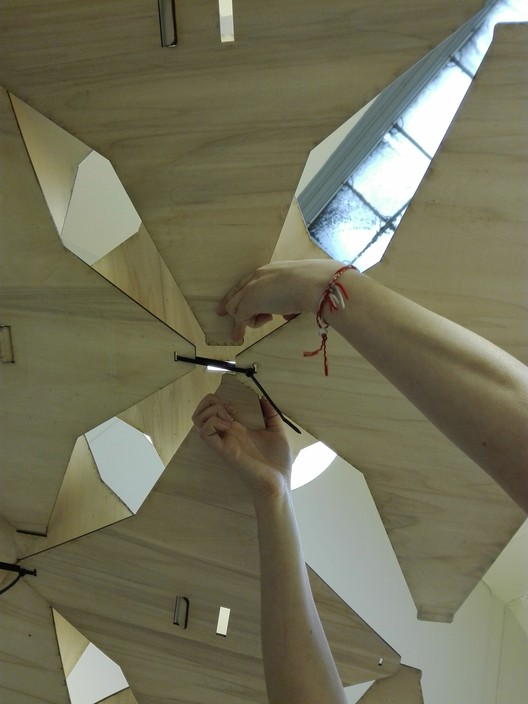
这种“自下而上”的方法允许根据经验工作;通过对其建构行为的直接物理测试,验证新的想法。 基于这种方式,展亭的设计并不是由一个整体的三维模型产生的,而是从迭代设计过程中获得,也就是说,先有组件才确定整体的形状。
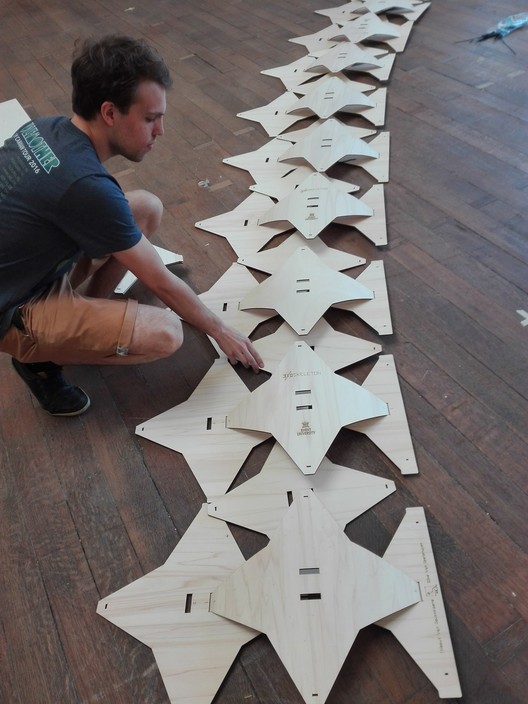
将这种自下而上的方法应用到结构设计中,使其无须定义好结构类型。 由于知识是在设计过程中逐渐积累起来的,所以这种方法可以用来研究创新的结构原则或某种材料的新应用。在这次设计过程中,对某一建筑的结构行为进行了实际的理解。
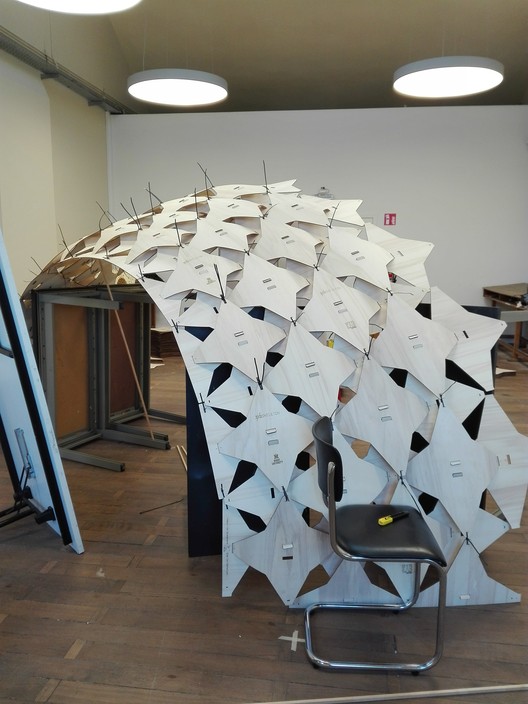
计算机辅助制造对这种方法有帮助,可以快速地制造大量的原型。这种快速的原型方法使我们能够快速地进行测试和学习。使设计过程可负担,只有在物理模型所用的材料便宜且制造技术快速的情况下才有可能。因此,从设计过程的开始就考虑了预算和制造技术的可获得性的局限性。
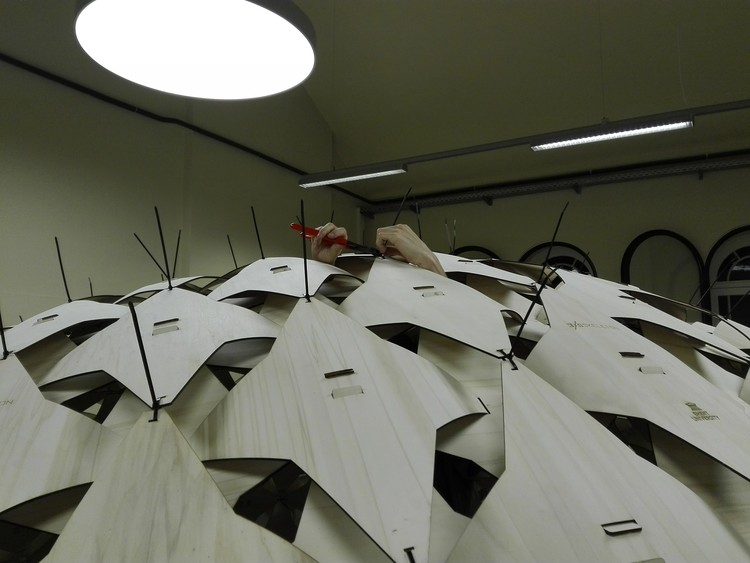
材料使用薄胶合木板,过程使用2D CNC 技术(切割机、铣床)。对材料的特性和物理行为的调查可以确定设计,因为这种自下而上的设计过程是从材料本身的可能性开始的。从最小的元素出发,研究出一种提升等级的结果和可能性。该设计的目标是在物理尺度模型、全尺寸原型和数字模型之间不断地交换信息。
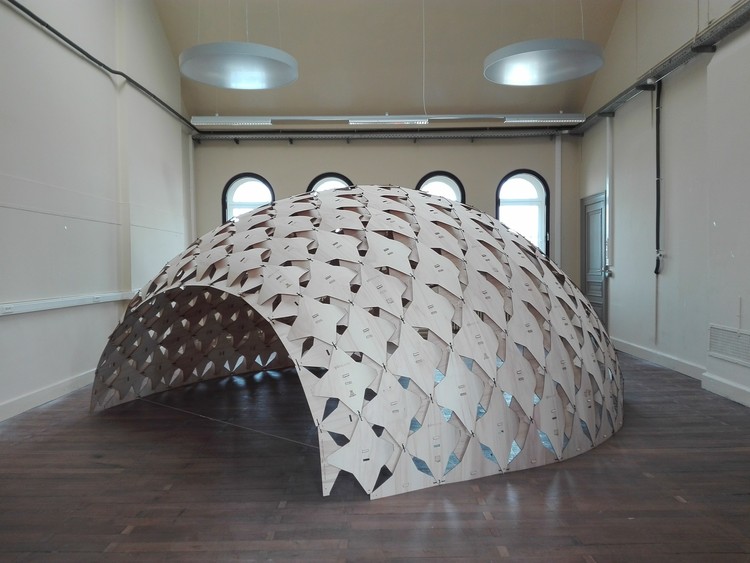
为了应用这种自下而上的设计方法,我们成功地研究了主动弯曲的创新结构原理。主动弯曲指的是一种特定材料的系统弹性变形,是静态结构的一种形式和自稳定的策略。通过处理这种自下而上的方法,可以在短时间内建造一个展示这种创新结构原则的展亭,并只使用有限的资源。我们设计了一个参数系统,而不是单个的展馆。通过将相同的组装系统应用到具有不同尺寸的设计模块中,可以生成不同的表面。
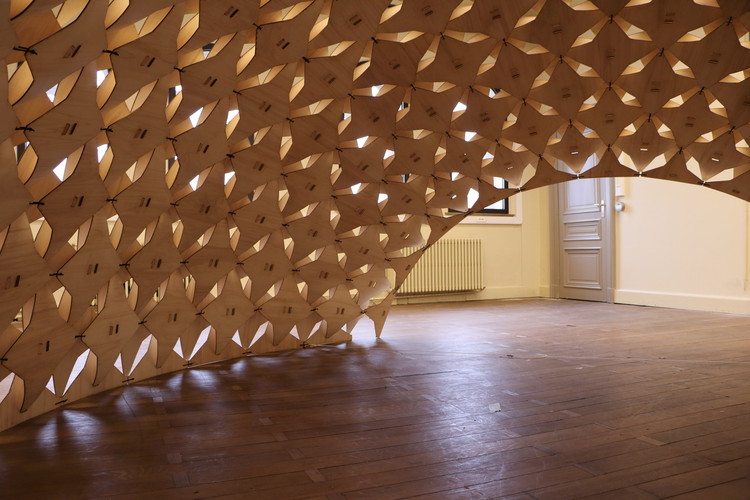
目标是在有限的时间内建造一个结构上具有挑战性的展亭,并使用有限的资源。 由于展馆不依赖于复杂的数字制作技术,因此每个人都可以访问。用一种自下而上的方法对结构设计进行快速原型设计将是实现这一目标的最有效方法。
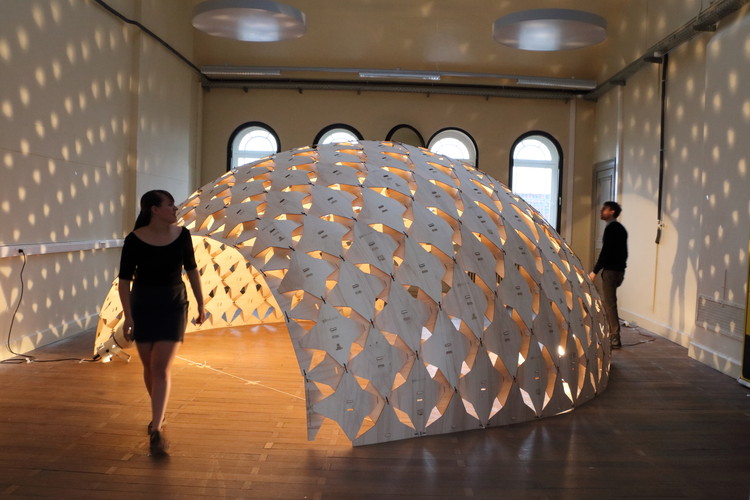
展亭本身的设计提出了具体的目标。 首先,组装和建造所需的资源量应尽可能地节约。这降低了总成本,并创造了一个负担得起的展馆。同时,展馆应该是手工制作的,并容易拆卸的。只有广泛使用的材料和制造技术才能被大量使用,使得这个展亭的组装成为大众的方便之物。
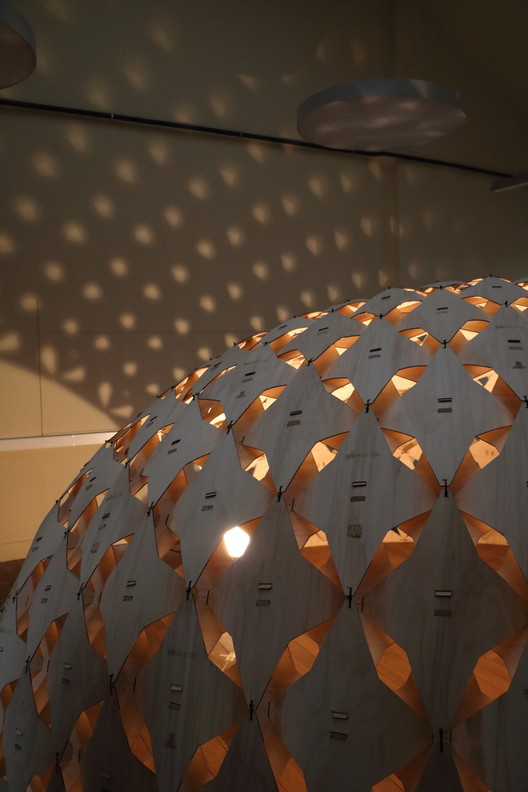
这篇硕士论文包含了一个精心策划的关于我们在自下而上的设计过程中所采取的不同步骤的概述,并遵循我们的整个工作流程。从最小的元素出发,研究的结果和可能性被研究成一个上升的等级,从平面进化到双曲面的亭子。 该设计是通过在全尺寸的木测试、纸原型和数字模型之间进行连续的信息交换来实现的。

展亭中只使用了两种连接件: 滑动关节和束带。
滑动关节将展亭内部的面板与外部的面板连接起来,是一种简单又优雅的解决方案。 由于面板是主动弯曲的,面板中的弹性力会将它们插入滑动关节。因此,这些关节非常简单,不需要像钉子或螺丝钉这样的附属部件。
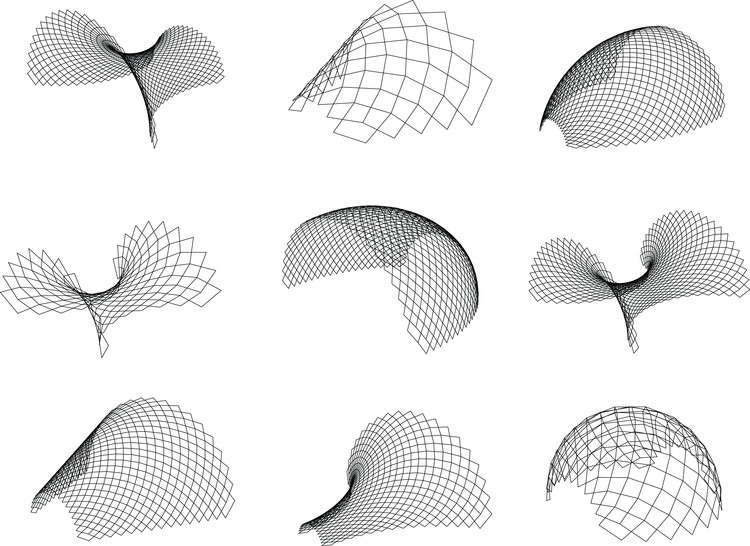
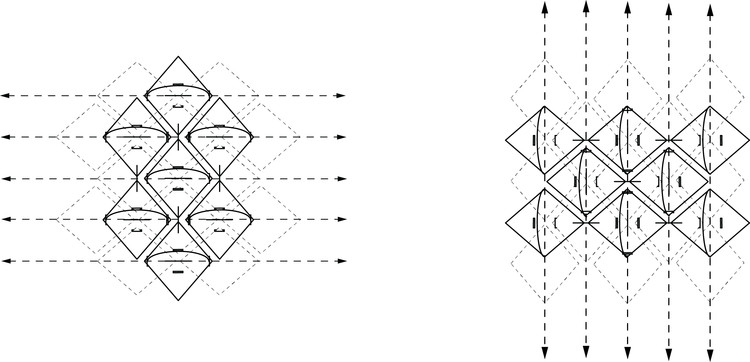
系带是用来保持面板在底板位置。可以快速方便地组装,但也可以作为一种重要的控制机制。施工过程中,组装的面板越多,展馆就越高,离最终的形状越近。因此,在施工过程中有必要建立一个可以逐渐加强的连接。系带是理想的解决方案。所有的面板都可以根据需要弯曲,当展馆升起时,带子可以进一步收紧。
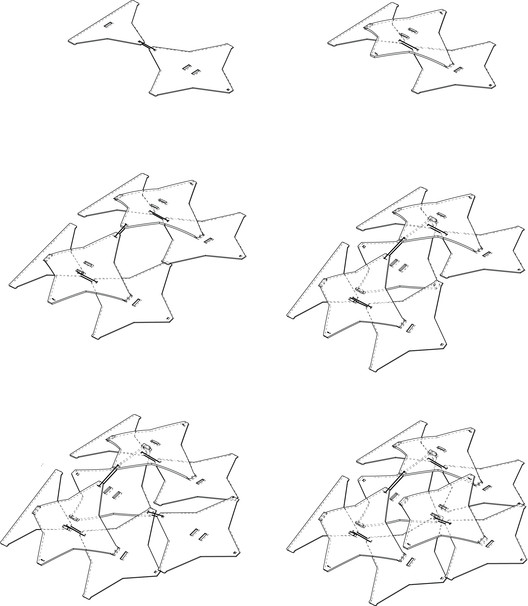
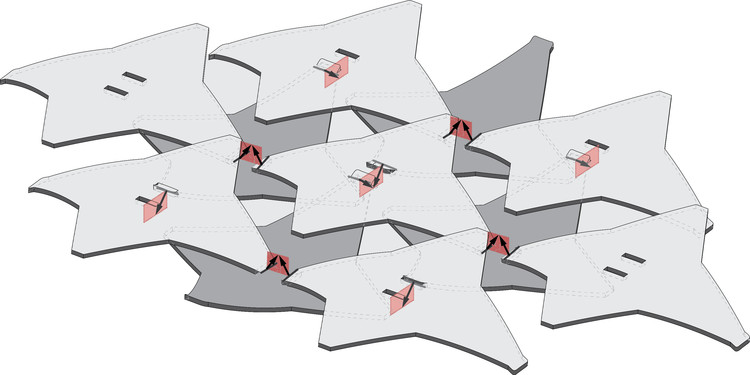
主持建筑师:Thibaut Van Dousselaere & Silke Van Geeteruyen
设计团队:Willem Bekers, Sebastiaan Leenknegt, Ruben Verstraeten, Arthur De Roover (University of Ghent, Department of Architecture and Urban Planning ), Jan Belis (Department of Structural Engineering), Stijn De Mil (Fablab Factory)
项目位置: 根特,比利时
项目年份:2017
项目面积:20 m2
摄影师:Jeroen Christiaen & Saskia De Mol